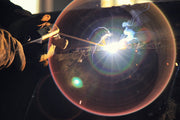
Slag inclusion formation ranks among the most pervasive and damaging defects in stick welding (Shielded Metal Arc Welding - SMAW). These non-metallic particles trapped within the weld metal or between weld beads compromise structural integrity, create stress concentration points, and accelerate corrosion. Preventing them demands a holistic strategy addressing electrode selection, technique refinement, parameter optimization, and meticulous cleaning. This guide delivers actionable, expert-backed methods to eliminate slag inclusions from your SMAW operations.
Understanding Slag’s Role and Slag Inclusions in Stick Welding
Slag formation is an inherent, beneficial outcome of stick welding. The flux coating on SMAW electrodes melts during welding, generating gaseous shielding and a molten slag layer. This slag performs critical functions:
-
Shielding Protection: Creates a physical barrier preventing atmospheric contamination (oxygen, nitrogen) of the molten weld pool.
-
Thermal Control: Insulates the solidifying weld, slowing the cooling rate to reduce brittleness and cracking risks.
-
Weld Bead Shaping: Influences bead contour and surface smoothness.
Slag inclusions occur when this slag fails to rise fully out of the weld pool before solidification or becomes mechanically trapped. They manifest as:
-
Linear or elongated streaks visible via radiography.
-
Spherical or needle-shaped non-metallic particles (oxides of calcium, silicon, aluminum) within the weld metal or at fusion boundaries.
-
Surface or subsurface defects, with subsurface inclusions requiring non-destructive testing (dye penetrant, X-ray) for detection.
Why Slag Inclusions Demand Zero Tolerance
-
Structural Weakening: Inclusions create voids and discontinuities, drastically reducing tensile strength and fatigue resistance. The weld becomes prone to cracking under load or stress.
-
Corrosion Hotspots: Trapped slag and adjacent crevices accelerate electrochemical corrosion, especially in pipelines or pressure vessels.
-
Porosity Catalyst: Slag pockets can trap gases, leading to interconnected porosity.
-
Costly Rework: Repair requires grinding out the defect and re-welding, increasing project time and cost significantly.
Primary Causes of Slag Inclusions in Stick Welding
A. Flux Composition and Electrode Type
The electrode's flux coating dictates slag behavior and inclusion risk:
Table 1: Electrode Flux Types and Slag Inclusion Risk
Flux Type | Key Components | Slag Behavior | Inclusion Risk | Best Applications |
---|---|---|---|---|
Rutile/Acid | High Titanium Dioxide (TiO₂), Silicates | Lower density, glassy slag. Self-detaching or easily removable. Forms flatter beads. | Low | General fabrication, easier positional welding, lower-skill applications |
Basic/Low-Hydrogen | Calcium Carbonate (CaCO₃), Calcium Fluoride (CaF₂) | Denser, adherent slag. Fast-freezing for position welding but difficult to remove. Forms convex beads prone to trapping slag. | High | Critical structures (pressure vessels, bridges), high-strength steels, hydrogen control |
High-Silicate | Silica (SiO₂) dominant | Glass-like, often self-detaching slag. | Low-Moderate | Applications requiring easy slag cleanup |
Iron Oxide | FeO additives | Lowers weld pool surface tension. Forms concave beads improving wetting. | Moderate | Flat/Horizontal positions where concavity aids slag release |
B. Incorrect Welding Parameters
-
Low Amperage/Current:
-
Problem: Insufficient heat prevents proper fluidity of the weld pool and slag. Slag trails behind instead of rising, becoming trapped.
-
Solution: Operate within the upper third of the electrode’s recommended amperage range. Ensure bright, crisp arc sounds.
-
-
Excessive Travel Speed:
-
Problem: The weld pool cools too rapidly before slag can float out. Slag gets "frozen" mid-migration, particularly at bead edges.
-
Solution: Maintain a speed allowing the slag to fluidly follow the arc, not run ahead. Visually confirm the molten pool stays behind the slag line.
-
-
Long Arc Length (High Voltage):
-
Problem: Increases voltage, widens the arc cone, and spreads heat input. Results in poor penetration, wider beads, undercut (trapping slag), and excessive spatter.
-
Solution: Hold a tight, consistent arc length (≈1/8" or electrode diameter). Listen for a steady crackling sound.
-
C. Poor Welding Technique
-
Improper Travel Angle (Push vs. Drag):
-
Critical Rule: "If there’s slag, you DRAG!"
-
DRAG Technique (Backhand): Electrode angled 0-15° back from perpendicular, pulling the weld. Positions the arc force and molten pool to push slag behind the solidifying bead, preventing it from running ahead or underneath.
-
PUSH Technique (Forehand): Electrode angled towards the direction of travel. Forces slag ahead of the weld pool, high risk of entrapment beneath the bead.
-
-
-
Incorrect Work Angle:
-
Problem: Angling too steeply (>20°) or inconsistently focuses heat unevenly, leading to undercut or uneven bead profile where slag pockets form.
-
Solution: Maintain consistent angles suited to joint geometry (e.g., 45° for fillets).
-
-
Erratic Travel Speed & Weave Issues:
-
Problem: Speeding up/slowing down creates inconsistent bead profiles and overlap points trapping slag. Dwell time too short at weave edges prevents sidewall fusion and flattens bead profile.
-
Solution: Practice consistent speed. When weaving, pause briefly (≈1 sec) at edges to ensure fusion and avoid deep pockets.
-
D. Inadequate Cleaning & Preparation
-
Skipping Interpass Slag Removal:
-
Problem: Failure to fully remove slag between passes traps it permanently beneath subsequent layers.
-
Solution: Mandatory cleaning after every pass.
-
-
Poor Base Metal Preparation:
-
Problem: Rust, oil, mill scale, paint, or moisture contaminate the weld pool, altering slag chemistry and behavior, increasing inclusion risk.
-
Solution: Grind/clean joint faces and adjacent areas (≥1") to bright, bare metal.
-
How To Avoid Slag Inclusions: Proven Prevention Strategies
1. Electrode Selection & Handling
-
Match Flux Type to Application: Use rutile (E6013, E7014) for easier slag control where feasible. Reserve basic (E7018) for critical joints only when low-hydrogen is mandatory. Preheat E7018 electrodes per spec.
-
Correct Size & Storage: Use the smallest practical diameter for better control. Keep electrodes dry (especially low-hydrogen) in a heated cabinet to prevent moisture-induced flux issues.
2. Optimizing Welding Parameters
-
Amperage: Set at the higher end of the electrode manufacturer’s range. Validate by:
-
Smooth arc transfer (no sticking/stubbing).
-
Slag easily peels behind the weld pool.
-
Adequate penetration without undercut.
-
-
Travel Speed: Adjust so:
-
The molten weld pool visibly stays behind the leading slag edge.
-
Slag flows smoothly onto the solidified bead without dripping into the pool.
-
-
Arc Length: Maintain consistently short (core wire diameter or less). Use the "crackling bacon" sound as an auditory guide.
Table 2: Parameter Adjustment Guide for Slag Inclusion Prevention
Symptom | Likely Cause | Correction |
---|---|---|
Slag running ahead of arc | Travel speed too slow OR Amperage too low | Increase travel speed OR Increase amperage |
Slag bubbling/boiling in pool | Amperage too high | Decrease amperage |
Slag stuck under bead edges | Undercut present | Reduce amperage, improve work angle, increase travel speed slightly |
Slag difficult to remove post-weld | Long arc length, Wrong electrode type | Shorten arc, Consider switching to rutile electrode |
3. Mastering Technique
-
Mandatory Drag Technique: Maintain 5-15° drag angle. Position yourself to comfortably pull the electrode along the joint
-
Controlled Bead Placement & Sequencing:
-
Avoid excessive convexity. Aim for flat or slightly concave beads.
-
Plan multi-pass sequences to ensure proper bead overlap and avoid deep crevices. Use grinder to flatten high spots between passes.
-
-
Weaving Best Practices: Limit weave width to ≤3x electrode core wire diameter. Employ a slight (≈1 sec) pause at weave extremes to ensure fusion and flatten profile.
4. Rigorous Cleaning Protocols
-
Interpass Cleaning is Non-Negotiable:
-
Cool First: Allow weld to cool sufficiently (hand-touchable). Hot slag is gummy and harder to remove.
-
Tool Selection:
-
Chipping Hammer: Remove bulk slag immediately after welding.
-
Stiff Wire Brush (Stainless for SS): Vigorous brushing along/against bead direction.
-
Needle Scaler: Effective for tight corners, crevices, and tenacious slag.
-
Grinding: Essential for basic electrodes (E7018), deep grooves, or highly convex beads. Creates a smooth, slag-free surface for next pass.
-
-
Verification: Visually and tactilely inspect. No shiny, glassy residue allowed.
-
-
Impeccable Joint Prep: Clean ≥1 inch on either side of the joint. Degrease and remove all scale/rust via grinding, sanding, or abrasive blasting.
Advanced Detection and Quality Assurance
-
Real-Time Monitoring: Utilize weld cameras (e.g., Xiris XVC series) to observe slag behavior relative to the arc and pool during welding. Allows immediate correction before inclusion occurs.
-
Post-Weld Inspection:
-
Visual Inspection (VT): Look for linear indications, roughness, or pinholes.
-
Dye Penetrant Testing (PT): Detects surface-breaking inclusions.
-
Radiographic Testing (RT): Identifies subsurface inclusions.
-
-
Adherence to Standards: Follow acceptance criteria (e.g., ISO 5817 Levels B, C, D) defining allowable inclusion sizes based on weld criticality.
Conclusion: Discipline Yields Flawless Welds
Preventing slag inclusions in stick welding hinges on methodical control over variables within the welder’s command. Electrode selection tailored to the job, precise parameter settings (prioritizing sufficient amperage and controlled speed), flawless technique (embracing the drag method and consistent manipulation), and uncompromising cleaning between every single pass form the bedrock of inclusion-free welds. While basic electrodes present higher challenges, their successful use in critical applications validates that meticulous adherence to these principles delivers structurally sound, durable results. Invest in the right tools (quality chippers, grinders, brushes), continuously refine technique through practice, and never underestimate the power of pristine preparation. By mastering these elements, welders transform slag—a necessary byproduct—from a potential defect source into a manageable protector of weld quality.
👋👋👋No matter what kind of welding machine you need, Doughty Welder can provide for your needs. Contact our sales team if you need advice beyond what this article provides. Our team of experts can help you make the right choice.
🧐🧐🧐You might like the following:
1.The Ultimate Battle: Arc Welding vs. Laser Welding
2. Why Welding with a TIG AC/DC Welder? The Ultimate Guide
3.Based on 4000+ customer reviews, this plate gold welding artifact stan